Detecting defects before they occur
How does vehicle data make predictive maintenance possible?
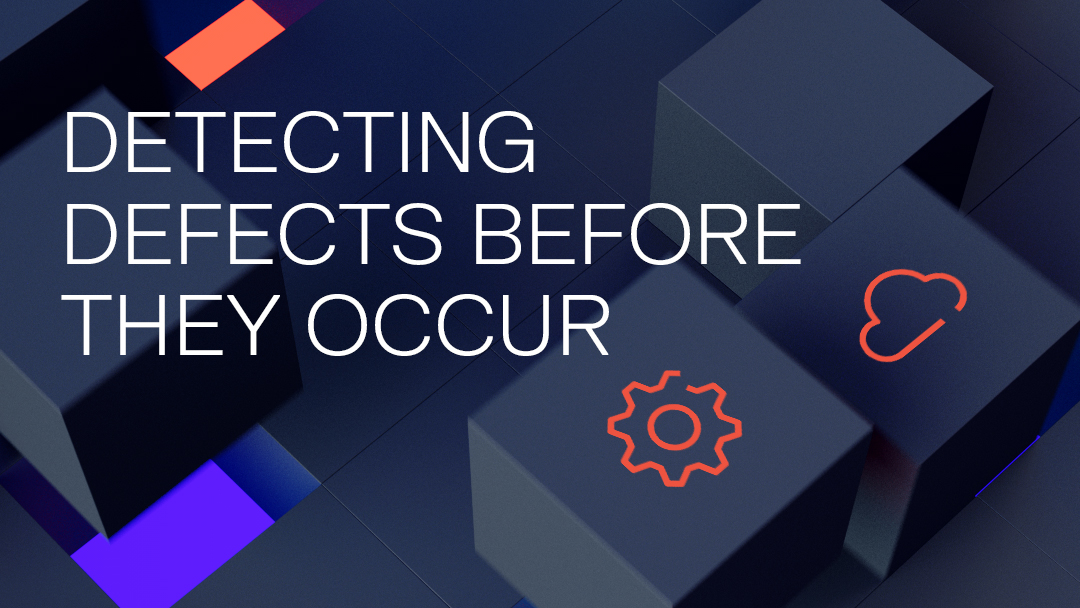
Data is an incredibly valuable resource. It allows for concrete solutions to be developed on the basis of real, traceable information and eliminates any assumptions and guesswork.
As vehicles become more intelligent and connected, they’re generating ever larger amounts of data, which opens up huge potential for predictive maintenance: determining – in advance – whether a part needs to be replaced or the vehicle needs to be serviced. Thanks to vehicle data, both drivers and workshops can receive a clear indication of the current condition of a vehicle and its individual components.
What is predictive maintenance?
Predictive maintenance is a targeted method that aims to identify potential issues before any faults or damage occurs. It can be very complex, having to rely on internet of things (IoT) technology, big data and cloud analytics. The payoff is that it’s very accurate and efficient in comparison to other methods.
These other methods are reactive maintenance and preventative maintenance. Reactive maintenance addresses a fault only after it’s happened. This means that there’s downtime when the vehicle is in the workshop. Preventative maintenance is planned, routine maintenance. While it might prevent a fault occurring, it’s not always efficient, economical or sustainable, with vehicle parts perhaps replaced too early.
How does it work?
In an automotive context, predictive maintenance considers various types of vehicle data, such as mileage, battery condition, tire pressure, air temperature and motor RPM. In some cases, even vehicle acoustics can be taken into account, with pattern-matching algorithms and frequency analyses detecting changes to normal operating sounds.
The data is gathered by vehicle sensors and processed by artificial intelligence. Together with an analysis of historical vehicle data, the system correlates this information to build a picture of the current condition of the vehicle and its individual components. If a part is shown to be failing, the customer could be presented with a description of the fault in the infotainment system of their car, for example. They could even be offered a suggested appointment date and time at their preferred service partner. Once the appointment request is sent, the service partner would receive the request in their inbox, together with an overview of the customer and vehicle data. The service partner can then get in contact with the customer and confirm the appointment.
Benefits
With predictive maintenance, the customer no longer has to stay on top of the service intervals for their car. Currently, they have to actively get in touch with the workshop and arrange an appointment if their car is due for a service, or if they suspected that something is broken. In future, it’ll be the other way around, and they’ll be contacted by the workshop. With more targeted appointments, customers can minimize downtime without a car and reduce any unwanted and untimely surprises.
Predictive maintenance also identifies issues that may otherwise go unnoticed. Data analytics is used to bring together all vehicle data and consider the system as a whole, while artificial intelligence can show exactly how and where the car has been driven. Perhaps a lot of harsh braking and acceleration has caused extra strain on the brake pads and motor. Or maybe driving on bad road surfaces and hitting potholes has led to greater tire wear, loss of pressure or additional strain on suspension.
Finally, predictive maintenance is also more economical and sustainable than other maintenance methods. It ensures that components that are still in good condition and have some life left in them are not unnecessarily replaced. More value can be extracted from components and the lifetime of the overall vehicle can be improved.