Predictive Maintenance: Anticipating what’s next
Making everyday life easier for drivers: With Predictive Maintenance, CARIAD is developing a service for the Volkswagen Group brands that uses artificial intelligence and data-driven models to predict future events, such as unexpected signs of wear and tear.
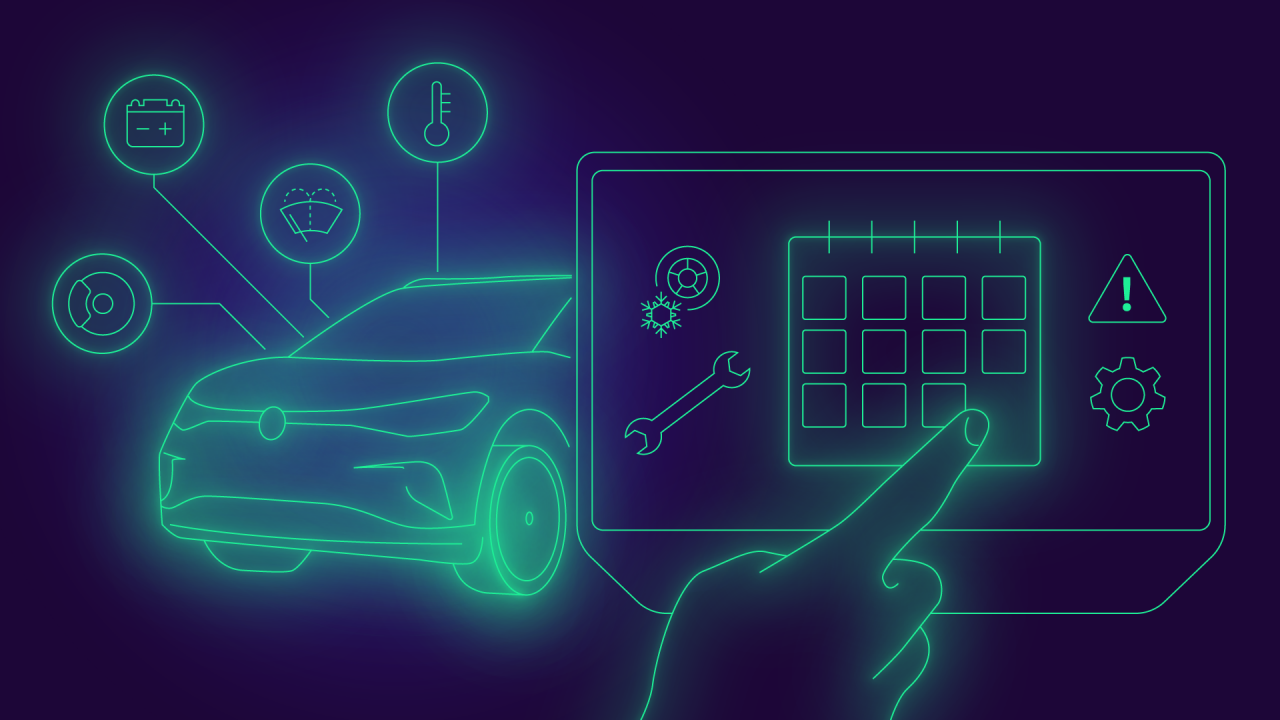
Making the mobility experience safer, more comfortable and more sustainable - this is what CARIAD teams work on every day with innovative software solutions. One example is the Predictive Maintenance service, developed by Amir Mulalic and his teams.
What is Predictive Maintenance?
"With Predictive Maintenance, we ensure that drivers are free from worries while on the road," explains Amir, Business Owner Car Maintenance Analytics. "Because they know that the manufacturer will take care of the maintenance of their vehicle – before they even realize it's due."
Predictive Maintenance is more accurate and efficient compared to other maintenance methods: For example, with "reactive maintenance", an issue is corrected after it has occurred, leading to downtime when the vehicle is in the workshop. The so-called "preventive maintenance" is a planned, routine service. Although this can prevent issues from occurring in the first place, it is still possible that certain vehicle components may need to be replaced shortly after maintenance due to undetectable wear.
How AI and data enable predictive maintenance
Predictive Maintenance uses machine learning to make the lives of drivers easier. The system analyzes data to predict future events, such as unexpected signs of wear. "Our goal is to identify potential issues accurately and efficiently before errors or damages even occur. To achieve this, we work closely with the Technical Development departments in the Volkswagen Group brands," says Milan Koch, Product Manager Predictive Maintenance at CARIAD.
An example: The sensors of a modern suspension system measure the movement of the shock absorbers and adjust them to the respective driving situation. In chassis function development, condition-describing characteristic values are calculated at high frequency in the vehicle based on the sensor signals. This pre-aggregated information is then pseudonymized and sent to the backend.
"There, our analysis tool works with computational models and complex machine learning algorithms," explains Milan. The tool compares the data with an intact shock absorber – and thus identifies abnormalities. For this purpose, more than 200 characteristic values are pre-processed, and a status decision is made with the help of various calculation algorithms.
If an anomaly is predicted, a service partner can proactively initiate a review and, if necessary, a repair. The customer receives a note in the infotainment screen with all maintenance-relevant information, including the option to book a workshop visit directly. There are hardly any limits to the use cases: "We are developing further prediction models throughout the Volkswagen Group, for example for high-voltage batteries, brakes or air conditioning systems," says Milan.
A look into the future: Remote diagnostics and remote repair
The team is already thinking ahead: "With the help of remote diagnostics, we can get an even deeper insight into the vehicle data and analyze it – even over a longer period of time and without being on site," says Christian Dremel, Product Manager Remote Services. In the future, this can make it possible that a vehicle does not even have to go to the workshop. Similar to the remote maintenance of a computer, experts can help solve an issue online via remote repair – before it even occurs.